STARCELL S.P.A. Quality and Innovation in the production of lightweight composite panels
MADE IN ITALY We produce in Italy in our high-tech plant in Calitri (AV)
Broad range of products We offer a broad range of panels with and without cosmetic finish, specifically designed for use in any industrial or manufacturing field.
Main fields of application construction, elevators, boating and shipbuilding, interior decoration, weight-reduction of marble and mosaics, rail and road transport
STARCELL®
Aluminium honeycomb, sandwich and lightweight composite panels, available as naked panel or faced with a wide range of materials and finishes (natural marble and granite, ceramic, HPL and CPL decorative laminates, solid surfaces, wood, stainless steel, special metals).
Our production is entirely Made in Italy. We distribute lightweight, sandwich, composite panels with cores which are both in aluminium honeycomb and in corrugated aluminium sheets or galvanised sheets.
Main fields of application: construction, elevators, boating and shipbuilding, interior decoration, weight-reduction of marble and mosaics, rail and road transport.
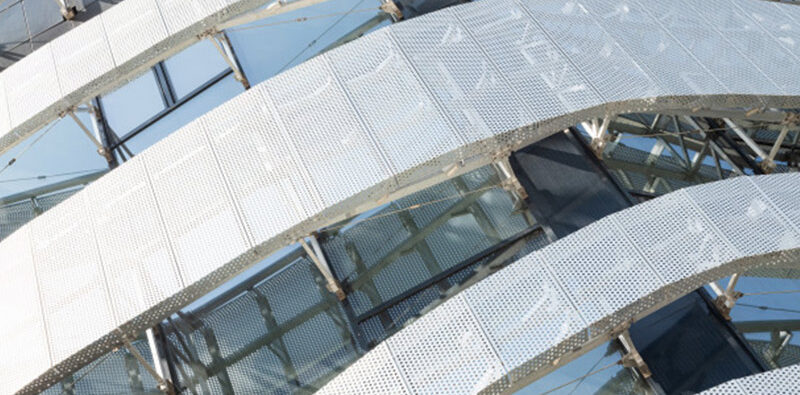
FIELDS OF APPLICATION
Starcell®’s panels are extensively used in many sectors ranging from construction to furniture, interior design and furnishings for residential or industrial use, but also for fitting out trains, ships, elevators, clean rooms and much more. Depending on the purpose, we can manufacture special panels that fully comply with international standards and regulations as well as customer-specific requirements.
PRODUCTS
PANELS WITH CORRUGATED CORE
Staluflex® is a sandwich panel with a corrugated aluminium sheet core or in galvanised steel produced by Starcell. A careful control on raw materials, on the completely automated process and above all innovative bonding allow Starcell to offer the market, with the same mechanical characteristics, a panel with a considerable advantage in terms of aesthetic quality, cost-effectiveness and guarantee over time. Staluflex® panels are used in construction, furniture, shipbuilding, railway and all those sectors where mechanical characteristics, lightness and fire resistance are required. Light, rigid, flat, incombustible, 100% recyclable, aesthetically free from surface defects, beautiful, Italian!
Staluflex® panels can be covered with a wide range of materials and finishes (natural marble and granite, ceramic, HPL and CPL decorative laminates, solid surfaces, wood, stainless steel, special metals).
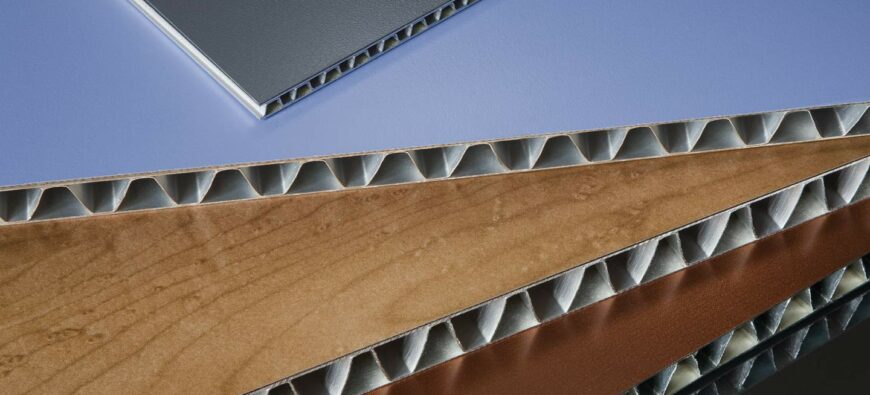
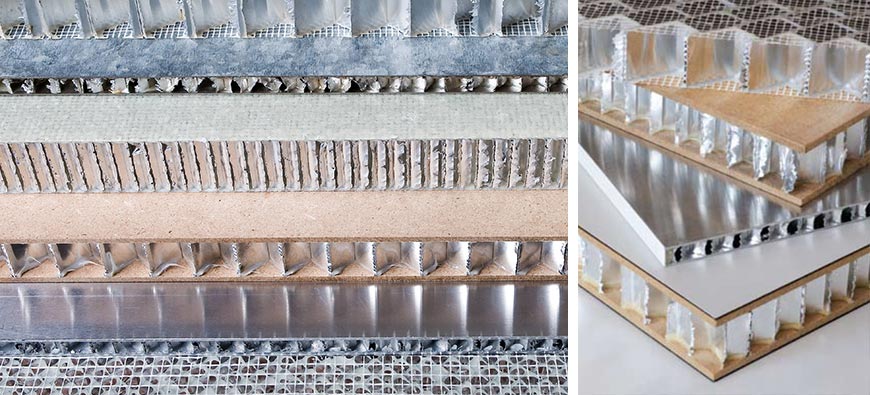
HONEYCOMB PANELS WITHOUT FINISH
Starcell® produces a wide of raw panels, i.e. without a cosmetic finish, which can subsequently be finished with a vast range of materials. Many different sizes and types of these panels are always in stock (skin material and thickness, density and thickness of the honeycomb, etc.).
HONEYCOMB PANELS WITH FINISH
Starcell can also provide an extensive range of panels with a cosmetic finish, ideal if the customer requires a product that is already finished and ready to use. The solutions we offer are the result of years of experience in gluing and processing materials on the raw substrates also thanks to our auxiliary partner companies, customers in case of marble and granite products. Our research is constantly progressing and we are advancing towards technologically innovative materials.
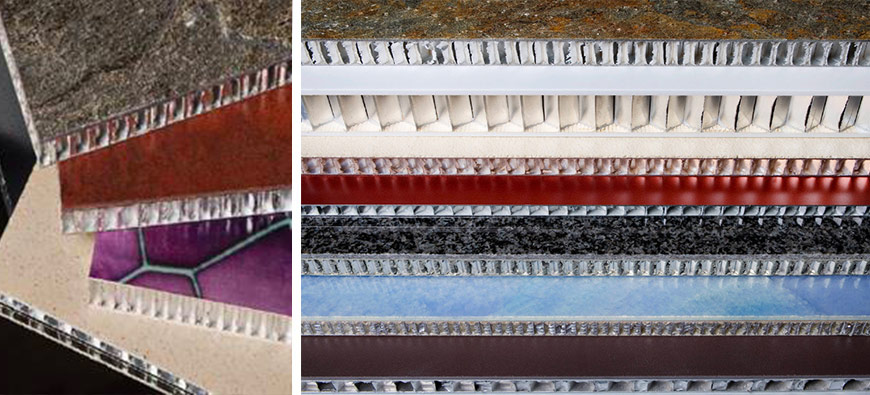
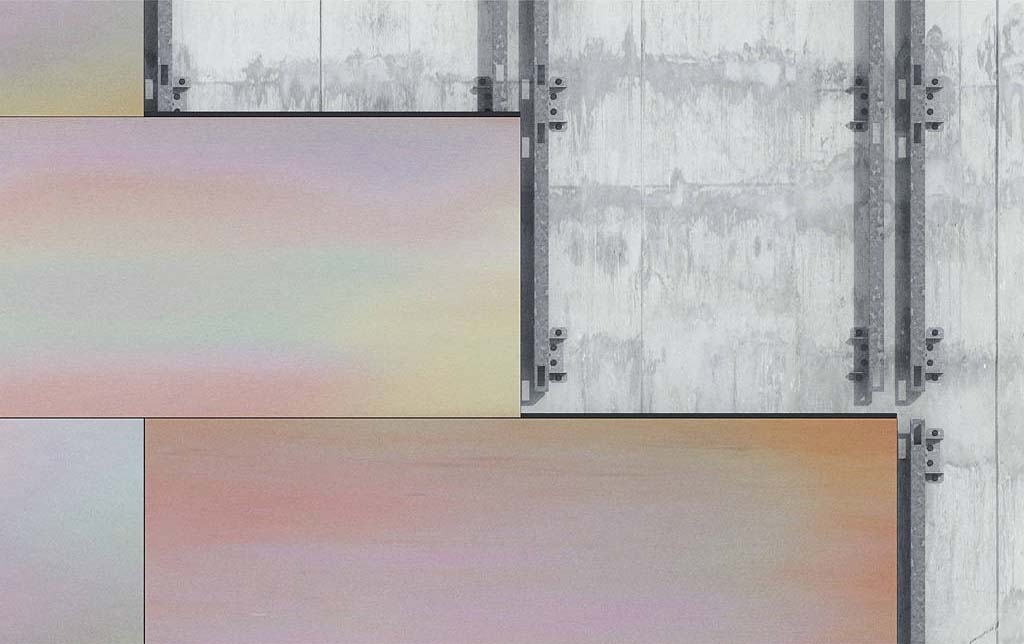
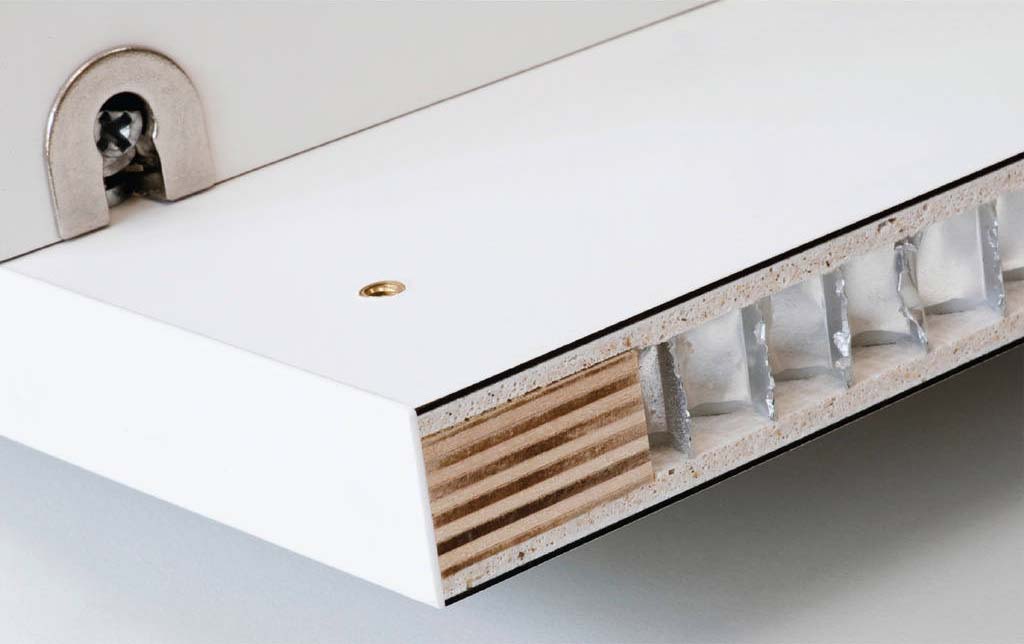
SPECIALITIES
Starcell®, which has always focused on research, has developed special solutions, specific for certain product sectors and fields of application, to offer new applications for sandwich panels, integrating them with fastening systems, edges, mechanical treatments, insertion of profiles, structural reinforcements and much more. All this with the aim of creating effective systems that go far beyond merely semi-finished products.
SERVICES
Processes and customization
All panels can be processed according to the requirements of the particular application. Starcell, either on its own or through its trusted, highly specialised partners, can perform any kind of operation on any type of panel and surface finish material, as required to produce a finished and completely customised product.
CUT TO MEASURE
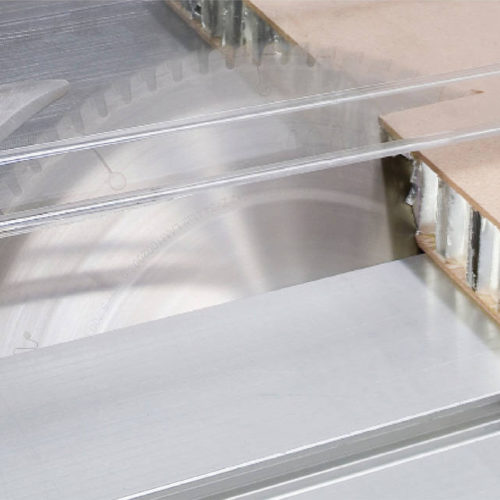
Composite panels require a variety of tools and equipment for cutting from time to time, depending on the type of skin used. We have a specific solution for every cutting requirement.
FINISHES
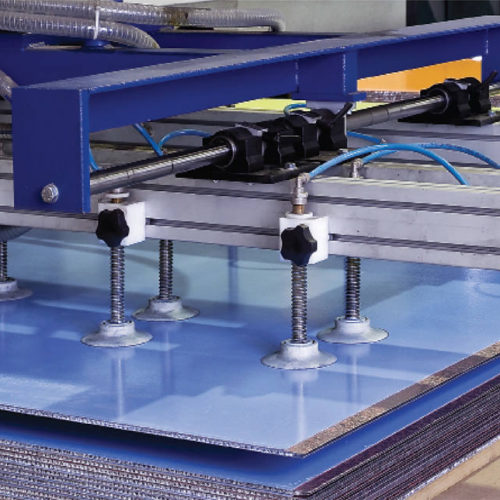
We have developed specific bonding solutions for each type of finishing material and substrate. Many finishing processes are automated to reduce production costs.
CNC PROCESSING
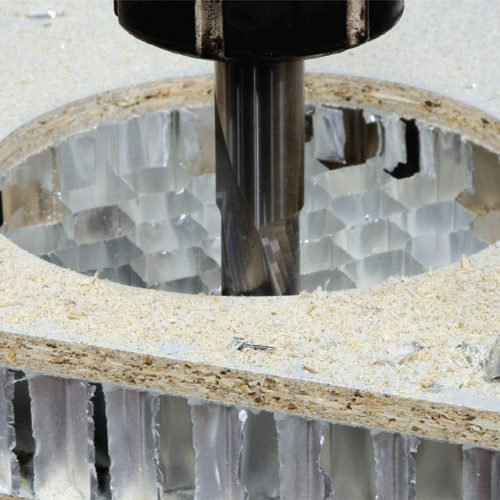
We are equipped with CNC machining centres to carry out any type of machining on our panels: through holes, slots, shaped milling, contouring, provisions for the application of threaded inserts and for the insertion of profiles or other accessories.
PHYSICAL AND MECHANICAL TESTS
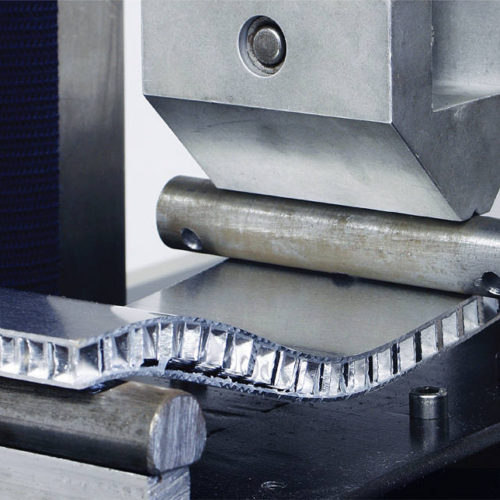
We can perform mechanical compression, traction, bending and tearing tests on-site and subject samples to climatic chamber tests to ensure the performance of custom products, as well as their stability and durability over time.
EDGES
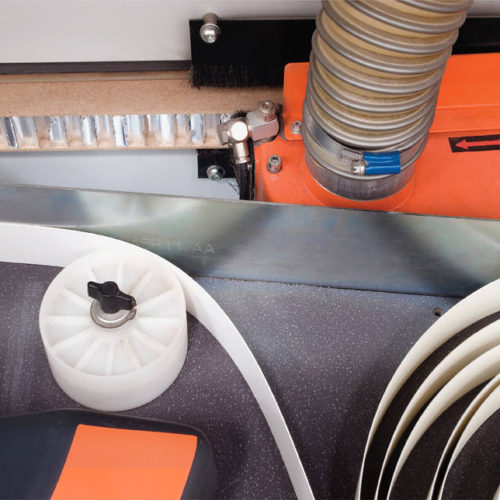
We can supply all the panels of our production complete with perimeter edging, performed in-house or by trusted specialists, according to the type of request.